4.29.2022 NON-POSTING NON-DISTRIBUTEDTHE ECF INGRESS STANDARD
Why
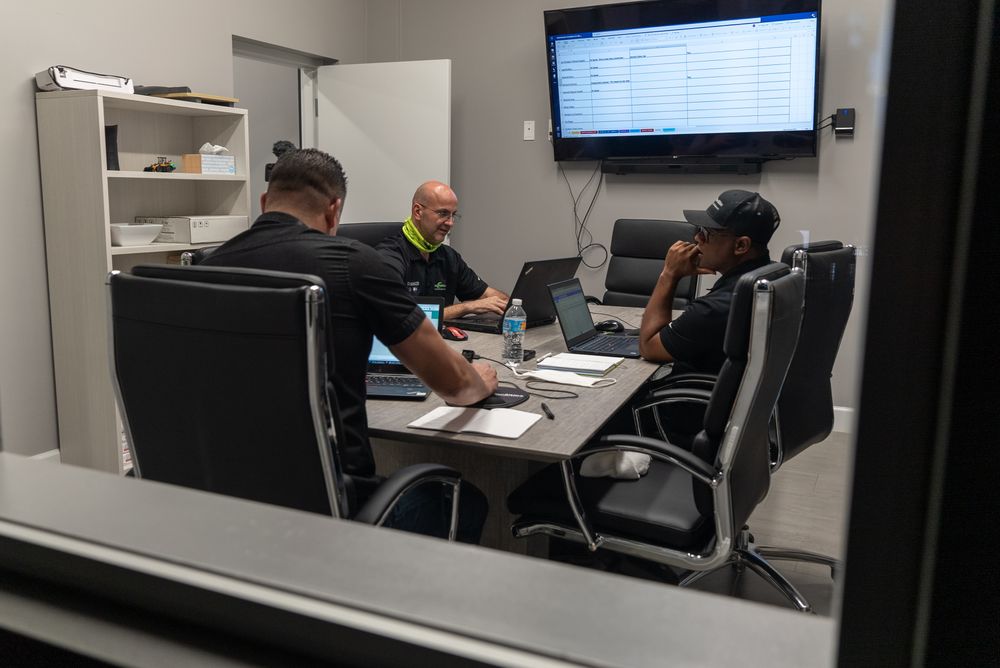
The ECF Ingress Standard holds the key to making the
ECF Egress Standard succeed. Through careful and well thought out planning, operations leaders can make all the necessary preparations for a proper start on the next business day. Our company culture on the matter is: “how we start, is how we end”.
“how we start, is how we end”
We started our day in an organized manner only because we were fully prepared the prior business day. We invested carefully in training and engaging our teams. Concluding our day should be handled in the same manner.
When we invest time in preparing, giving clear communication, and work to be resourceful as managers, we are in turn setting a very good example for our Crew Leaders. Our goal is to develop Crew Leaders and doing so starts with us as managers.
The Standard
(1) Re-Shuffle
Operations create best-effort schedules weeks in advance. But on any given workday many things can happen that require the pre-established plan to be adjusted for the next business day's production plans. What kinds of things can occur that require the adjustment? Here are just a few examples:
- A crew may not finish a job as intended
- A crew may run out of materials on a job before completion
- An employee may notify their supervisor of their need to take the next day off
- Equipment could fail
- Inclement weather may be forecasted that will impact production
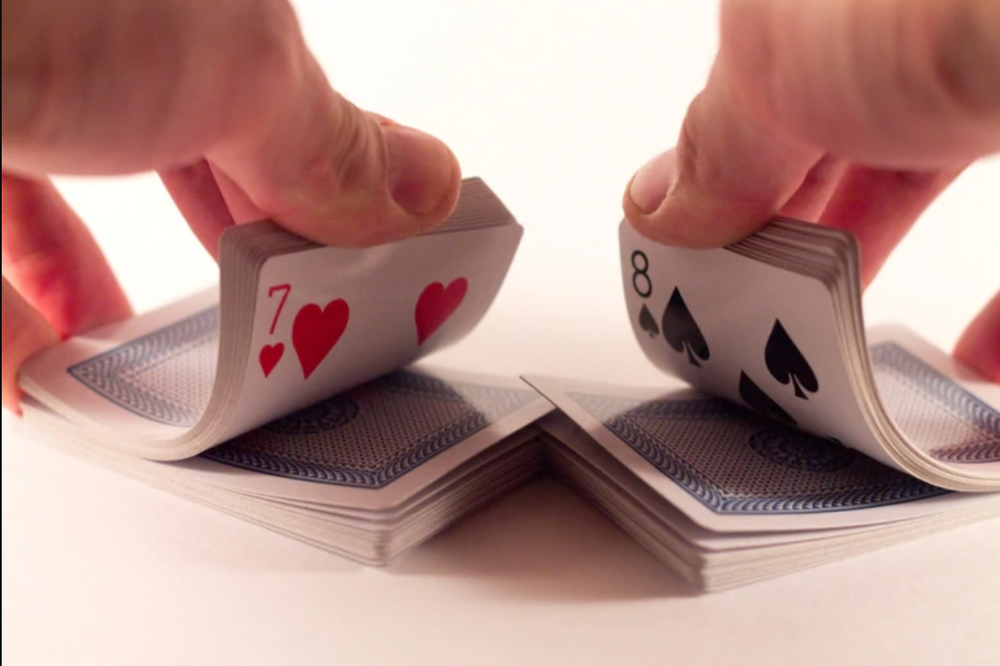
It is necessary for Operations to
"reshuffle the deck" to prepare for the next day. This means that in a sense managers take a step back with their current knowledge of the needs of the operation and reshuffle or reorganize their resources based on the production needs for the following business day.
This best practice should be done by 3 PM each business day, therefore, providing enough time for the remaining steps of the Standard to be followed.
Systems that assist an operations manager to perform the reshuffle include, real-time knowledge of field conditions, an updated and accurate Default Schedule, non-contract work ticket backlogs, and real-time knowledge of customer requests.
(2) Pre-Arrival Communications
Pre-arrival communications are different from ongoing field reconnaissance, phone calls, or social feed monitoring with Crew Leaders and Field Supervisors. Pre-arrival communications are scheduled phone or video calls with Crew Leaders and Field Supervisors to advise them of what their most current schedule is for the following business day. These calls will aid the leader to be ready to properly prepare for the following business day as soon as they arrive at the Company location.
What type of information should a manager be ready to share with the leader when they contact them?
- What job site they will be working on
- What type of work they will be doing
- If they need any specialized equipment and why
- Who will be on their crew
- Any specific job instructions that may apply
It is understood that communicating with special services crews may be more complicated and require more advanced preparation than crews who perform recurring tasks such as mow crews. Your goal is to make sure the Crew Leader or Field Supervisor is ready to re-focus efforts to the next business day as soon as they arrive at the Company location.
(3) Resource Staging & Preparations
Managers use the hours leading up to the arrival of returning crews to the Service Center to ensure they have all materials and specialized equipment ready for loading upon Ingress.
If one or more items cannot be loaded at night due to security concerns, they should be staged in an area that is easily accessible, and known to the Crew Leader for loading first thing in the AM immediately following the Crew Leader Muster.
Other direct ship equipment and materials can be sent to job sites as needed, and should not impact the ingress or egress standards of operation.
(4) Arrival & Re-Focus
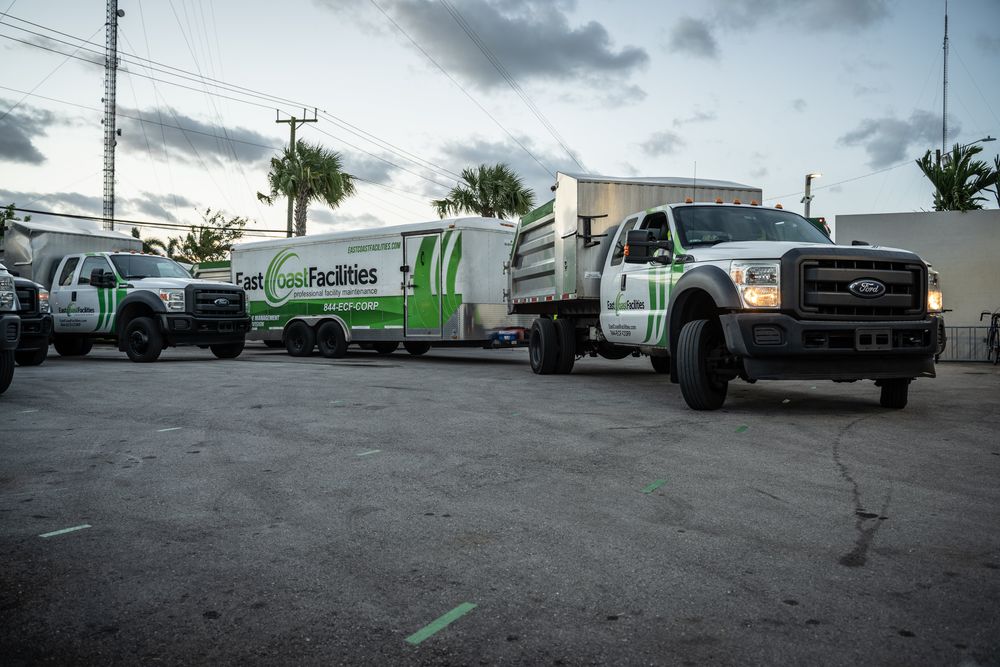
Upon arrival Crew Leaders immediately begin with a re-focus of efforts for the following business day. Because of good communication according to the Standard, they already know what to load onto their trucks for the next day.
Operations will advise Crew Leaders as to when they should wash their truck or trailer and perform necessary equipment maintenance or repairs. Crew Leaders should not conduct these types of operations without direction.
Once each Crew Leader completes his re-focus efforts, he may punch out for the day. It is at the discretion of management whether a Crew Leader needs the assistance of some or all of his crew for re-focus efforts.
(5) Lockdown
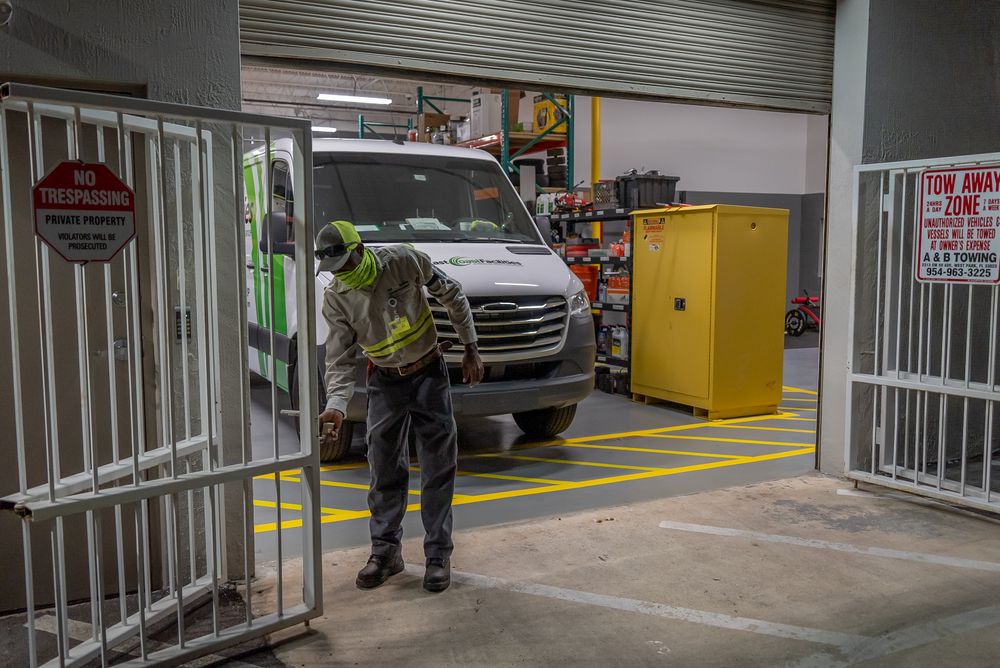
When the last crew completes its re-focus efforts for the day and all trucks are properly parked in their designated parking spots the facility will be locked down. This means all access points will be locked, all gates will be shut, and if an alarm system exists it will be activated.
Unlike the attendance requirements for The Egress Standard, not all operations managers are required to be present for Lockdown. Generally, the Director of Operations and the Operations Manager role will create a rotating schedule to ensure at least one leader is present for Lockdown at or above the rank of Field Supervisor.
Crew Leaders should not be allowed to lock down a Company location.
Frequently Asked Questions
Question | Answer |
How should the Standard be implemented for direct report job sites? | Points 1 and 2 above should occur with no adjustment.
Point 3 "Resource Staging & Preparations" occurs by a designated manager arranging the delivery of materials or equipment as needed directly to the job site the day before it is needed unless it is more productive to have delivery occur the day of production.
Point 4 "Lockdown" occurs with a virtual confirmation between the highest-ranking onsite employee and the designated manager. Virtually constitutes a phone or video call for confirmation and completion of equipment and staging lockdown and security requirements.
|